Discover What is Porosity in Welding and Its Result on Architectural Honesty
Discover What is Porosity in Welding and Its Result on Architectural Honesty
Blog Article
The Science Behind Porosity: A Comprehensive Guide for Welders and Fabricators
Understanding the complex systems behind porosity in welding is crucial for welders and makers pursuing impressive craftsmanship. As metalworkers explore the depths of this sensation, they discover a globe governed by numerous variables that affect the formation of these minuscule voids within welds. From the composition of the base materials to the complexities of the welding process itself, a wide variety of variables conspire to either worsen or minimize the visibility of porosity. In this extensive guide, we will unravel the scientific research behind porosity, exploring its results on weld top quality and unveiling progressed techniques for its control. Join us on this journey via the microcosm of welding flaws, where precision meets understanding in the quest of flawless welds.
Comprehending Porosity in Welding
FIRST SENTENCE:
Assessment of porosity in welding discloses vital understandings into the integrity and quality of the weld joint. Porosity, defined by the presence of cavities or voids within the weld metal, is an usual problem in welding procedures. These gaps, otherwise properly dealt with, can jeopardize the architectural integrity and mechanical homes of the weld, bring about possible failings in the finished item.
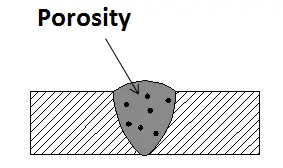
To discover and measure porosity, non-destructive screening approaches such as ultrasonic screening or X-ray inspection are commonly employed. These strategies permit the identification of internal defects without compromising the integrity of the weld. By evaluating the size, form, and circulation of porosity within a weld, welders can make educated decisions to improve their welding procedures and attain sounder weld joints.
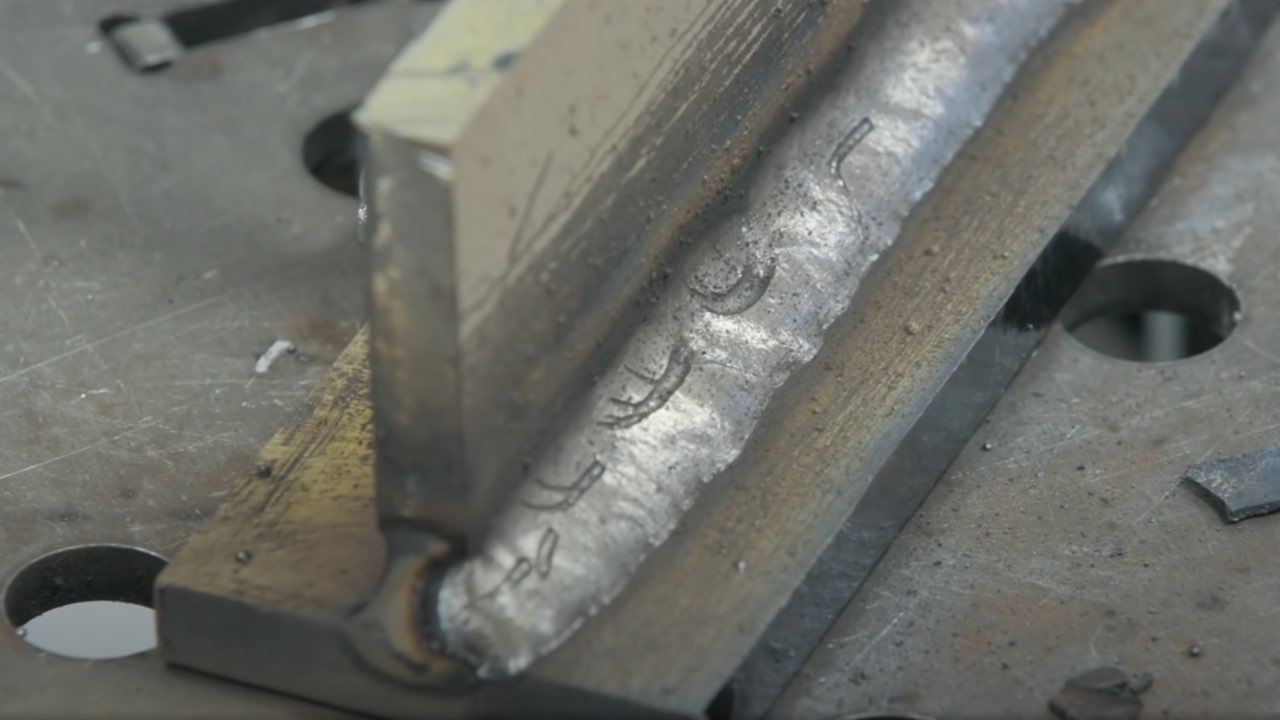
Variables Affecting Porosity Development
The incident of porosity in welding is influenced by a myriad of elements, ranging from gas shielding performance to the ins and outs of welding parameter setups. Welding criteria, consisting of voltage, current, travel speed, and electrode kind, also influence porosity formation. The welding technique employed, such as gas metal arc welding (GMAW) or secured metal arc welding (SMAW), can influence porosity formation due to variants in warmth distribution and gas coverage - What is Porosity.
Effects of Porosity on Weld Quality
Porosity development significantly jeopardizes the structural honesty and mechanical buildings of bonded joints. When porosity is present in a weld, it produces gaps or cavities within the product, decreasing the overall toughness of the joint. These gaps work as tension concentration points, making the weld a lot more at risk to fracturing and failing under tons. The existence of porosity additionally compromises the weld's resistance to corrosion, as the entraped air or gases within the gaps can react with the surrounding atmosphere, resulting in additional info destruction with time. Additionally, porosity can impede the weld's ability to withstand stress or influence, further endangering the total high quality and reliability of the welded framework. In vital applications such as aerospace, auto, or structural building and constructions, where safety and security and toughness are critical, the detrimental impacts of porosity on weld top quality can have serious repercussions, emphasizing the importance of reducing porosity with proper welding methods and treatments.
Strategies to Minimize Porosity
To boost the top quality of welded joints and guarantee architectural integrity, welders and producers utilize certain methods targeted at decreasing the formation of spaces and dental caries within the product throughout the welding process. One effective technique to lessen porosity is to guarantee proper product prep work. This consists of extensive cleaning of the base steel find here to remove any type of contaminants such as oil, oil, or moisture that might add to porosity development. In addition, making use of the appropriate welding specifications, such as the correct voltage, present, and take a trip speed, is critical in protecting against porosity. Preserving a constant arc size and angle during welding also helps in reducing the probability of porosity.

Moreover, picking the best protecting gas and keeping proper gas flow rates are necessary in minimizing porosity. Utilizing the ideal welding strategy, such as back-stepping or utilizing a weaving motion, can also help disperse heat uniformly and reduce the chances of porosity development. Ensuring proper ventilation in the welding setting to get rid of any prospective sources of contamination is important for accomplishing porosity-free welds. By implementing these strategies, welders can successfully lessen porosity and generate top quality bonded joints.
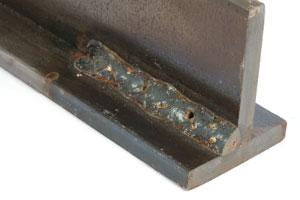
Advanced Solutions for Porosity Control
Carrying out innovative technologies and cutting-edge approaches plays a pivotal function in accomplishing premium control over porosity in welding processes. One advanced solution is using innovative gas combinations. Protecting gases like helium or a blend of argon and hydrogen can help minimize porosity by giving better arc security and improved gas coverage. In addition, using innovative welding techniques such as pulsed MIG welding or changed ambience welding can likewise assist mitigate porosity issues.
One more advanced remedy entails using sophisticated welding devices. Using devices with built-in attributes like waveform control and innovative power sources can boost weld top quality and decrease porosity risks. The execution of automated welding systems with precise control over specifications can dramatically minimize porosity problems.
Additionally, incorporating innovative surveillance and evaluation modern technologies such as real-time X-ray imaging or automated ultrasonic screening can help in detecting porosity early in the welding procedure, enabling prompt restorative browse this site activities. Generally, incorporating these advanced solutions can considerably boost porosity control and boost the general top quality of bonded parts.
Final Thought
Finally, comprehending the science behind porosity in welding is vital for welders and fabricators to create high-grade welds. By recognizing the variables affecting porosity development and carrying out techniques to reduce it, welders can boost the total weld quality. Advanced services for porosity control can even more enhance the welding process and make certain a solid and dependable weld. It is vital for welders to continually enlighten themselves on porosity and apply ideal techniques to attain ideal outcomes.
Report this page